
Stresses in press dies are usually high, but there is very little impact load so harder die can be used without the risk of breakage that might be experienced on a power hammer. This can reduce weight and subsequent machining. Mechanical presses are best suited for low profile forgings and usually incorporate knockout/liftout pins in the dies which automatically eject the forging from the die allowing the die, and thus the forging, to be designed with less draft allowance. Such an event can cause severe damage to the press or, in the least, substantial downtime to “burn” the dies apart to free the press. Because the stroke is a fixed length, care must be taken to ensure that the closure allowed is not so small as to risk having the press “stick” at the bottom of the stroke, and not complete the stroke.

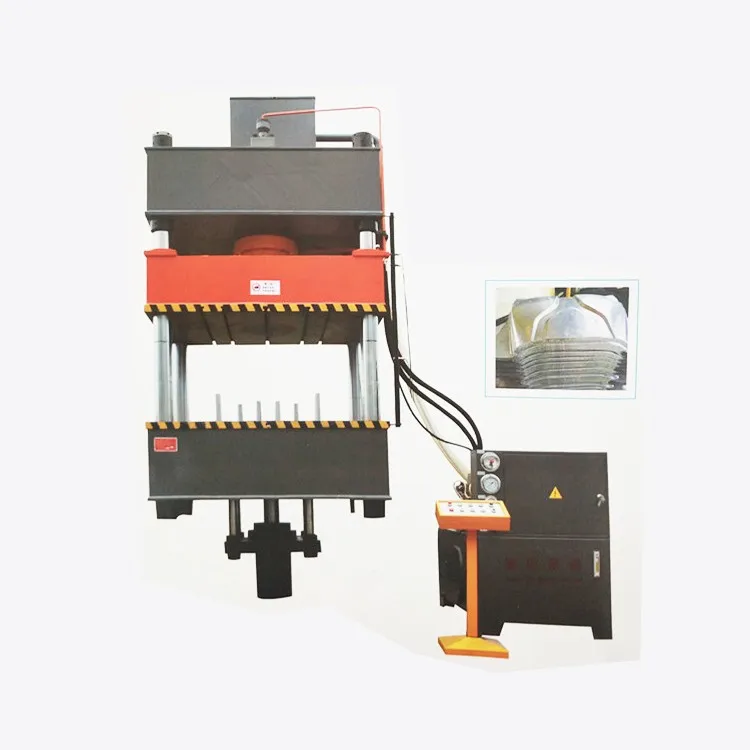
Ram speed is greatest at the center of the stroke, but maximum force is not achieved until near the bottom of the stroke. In general, presses can produce all of the same types of forgings produced on hammers and, in addition, can forge some alloys of moderate ductility that would shatter under the fast impact of the hammer die.ĭriven by a motor and controlled with an air clutch, mechanical presses have a full eccentric type of crankshaft that imparts a constant length stroke to a vertically operating ram. Mechanical Forging Presses generally incorporate a ram that moves in a vertical direction to exert a squeezing action on the work piece, in contrast with the repeated blow characteristics of hammer forging.
